Pipe fittings are essential components used in a wide range of applications across various industries. Their primary purpose is to connect, control, redirect, and adapt the flow of fluids or gases within piping systems.
Here are some of the primary applications of pipe fittings:
- Plumbing Systems: Pipe fittings are extensively used in plumbing systems for residential, commercial, and industrial buildings. They are used to connect pipes of different materials and sizes, create junctions, and route water supply, drainage, and sewage systems.
- Heating, Ventilation, and Air Conditioning (HVAC): Pipe fittings play a crucial role in HVAC systems for heating and cooling buildings. They are used to connect pipes carrying hot water, chilled water, refrigerant, or steam to heating and cooling equipment, radiators, air handlers, and distribution networks.
- Gas Distribution: Pipe fittings are used in gas distribution systems for residential, commercial, and industrial applications. china pipe suppliers They are used to connect gas pipes to appliances such as stoves, furnaces, boilers, water heaters, and industrial equipment that rely on natural gas or propane.
- Oil and Gas Industry: In the oil and gas industry, pipe fittings are used in exploration, production, refining, and transportation operations. They are used to connect pipelines, wellheads, production equipment, storage tanks, and processing facilities for the extraction, processing, and distribution of oil, natural gas, and other hydrocarbons.
- Chemical Processing: Pipe fittings are employed in chemical processing plants for transporting and controlling the flow of chemicals, acids, solvents, and other fluids. They are used in pipelines, reactors, distillation columns, storage vessels, and other equipment involved in chemical manufacturing and processing.
- Water Treatment and Distribution: Pipe fittings are used in water treatment plants and distribution networks for supplying clean drinking water and managing wastewater. They are used to connect pipes carrying treated water, chemicals, and additives to filtration units, pumps, valves, and distribution pipelines.
- Fire Protection Systems: Pipe fittings are critical components of fire protection systems in buildings and industrial facilities. They are used to connect sprinkler systems, standpipes, fire hydrants, and fire suppression systems to water supplies, ensuring rapid response in the event of a fire.
- Food and Beverage Industry: Pipe fittings are used in food and beverage processing plants for transporting and processing ingredients, liquids, and beverages. They are used in pipelines, tanks, mixers, pasteurizers, and packaging equipment, ensuring hygiene and sanitation standards are maintained.
- Mining and Mineral Processing: Pipe fittings are utilized in mining operations for conveying water, slurry, chemicals, and other fluids in mining and mineral processing operations. They are used in pipelines, pumps, crushers, chinese iron pipes and processing equipment for extracting and processing minerals and ores.
- Agriculture and Irrigation: Pipe fittings are used in agricultural irrigation systems for distributing water to crops, fields, and greenhouses. They are used to connect pipes, valves, sprinklers, and drip irrigation systems, ensuring efficient water distribution and crop cultivation.
These are just some of the primary applications of pipe fittings, demonstrating their versatility and importance in various industries and infrastructure systems.
How do pipe fitting accommodate changes in pipe direction?
Pipe fittings accommodate changes in pipe direction through various types of fittings designed for specific purposes. Here are some common pipe fittings used to facilitate changes in pipe direction:
- Elbows: Elbows are one of the most common types of pipe fittings used to change the direction of piping. They come in different angles, such as 45 degrees or 90 degrees, allowing pipes to turn at specified angles. Elbows are available in various materials, including metal, PVC, and CPVC, to suit different applications.
- Tees: Tees are fittings that allow pipes to branch out in different directions. They feature a T-shaped design with one inlet and two outlets, jianzhi pipe fittings or vice versa, allowing for the connection of three pipes at a junction. Tees are commonly used in plumbing, HVAC, and process piping systems.
- Reducers: Reducers are fittings used to transition between pipes of different diameters. They typically feature one end with a larger diameter and one end with a smaller diameter, allowing for the connection of pipes with different sizes while maintaining fluid flow. Reducers can be concentric (with the same centerline) or eccentric (with offset centerlines).
- Wyes: Wyes are similar to tees but have a Y-shaped design, allowing pipes to branch out at a 45-degree angle rather than perpendicular. They are commonly used in drainage and sewage systems to facilitate smooth flow and prevent clogging.
- Crosses: Crosses are fittings that allow pipes to intersect each other at 90-degree angles. They feature four openings arranged in a cross shape, allowing for the connection of four pipes at a junction. Crosses are commonly used in industrial piping systems and process applications.
- Bends: Bends, also known as sweeps or curves, are fittings used to change the direction of piping gradually. Unlike elbows, which have sharp turns, bends have a more gradual curve, reducing flow resistance and pressure drop. Bends are commonly used in fluid handling systems where smooth flow is essential.
- Couplings: Couplings are fittings used to join two pipes together in a straight line. While they do not change the direction of piping on their own, pipe fitting manufacturer couplings are often used in conjunction with other fittings to accommodate changes in direction. Couplings come in various designs, including compression couplings, threaded couplings, and slip-on couplings.
By using these types of pipe fittings strategically, engineers and plumbers can design piping systems that efficiently accommodate changes in direction while maintaining the integrity and functionality of the system.
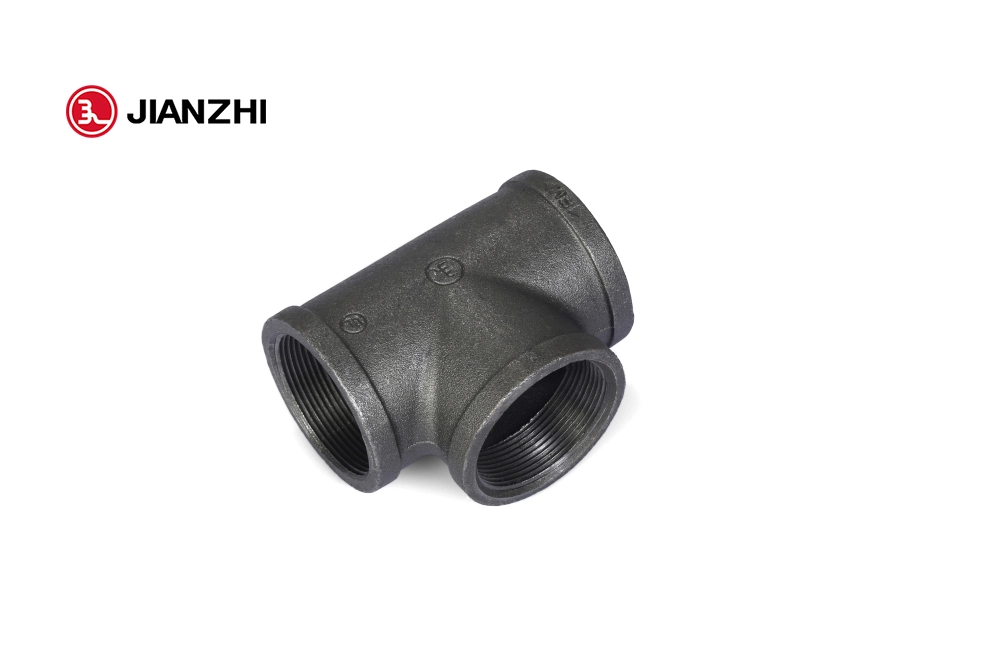